![Three Principles [India Trip Blog 3]](https://d24slhcvzhzz82.cloudfront.net/old_images/caltech_as_it_happens/6a0105349b8251970b01539153f637970b.jpg)
Three Principles [India Trip Blog 3]
The Art Center students do market research before every project, so they gave us a few tips before we got to our first field site.
We need to focus on understanding the problem, not thinking of solutions. When we visit a shop or factory, we have to work with three principles:
-
Be open-minded. Don’t come with preconceptions.
-
What people say and what people do is not always the same. For example, a worker might say he enjoys his job because he wants to give the right answer even if he / she clearly doesn’t.
-
Look for problems, not solutions. If you only see the biggest problems and begin focusing on solutions too fast, you might miss other important aspects!
Our first visit was to the Rubber Research Institute of India. The director of research, Dr. Nazir, gave us a brief overview of rubber trees, rubber tapping, and rubber in the economy. The trees take 7 years to grow and then yield around 25 years. Rubber, a mix of isoprenes, employs 0.4 million workers annually in India. However, about 65 percent of the world rubber consumption is SR (synthetic rubber). This has much higher CO2 emissions than NR (natural rubber). RRI is attempting to increase the rubber output of Indian farmers; they already have several tree species that are higher yielding which they give the farmers. They would like to see better fungicides to protect the trees. They are also designing new products for rubber, such as better shoe soles for people with leprosy.
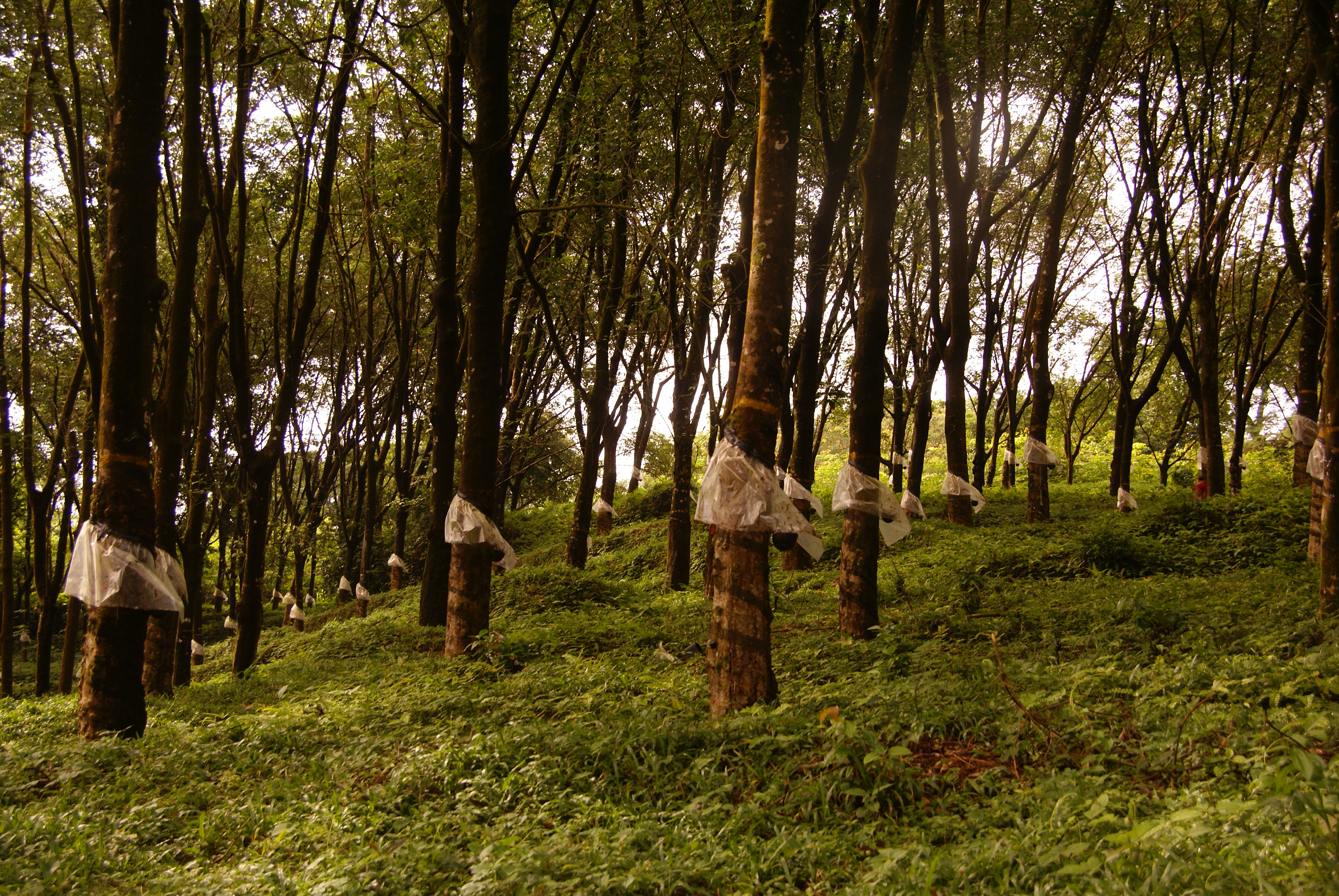
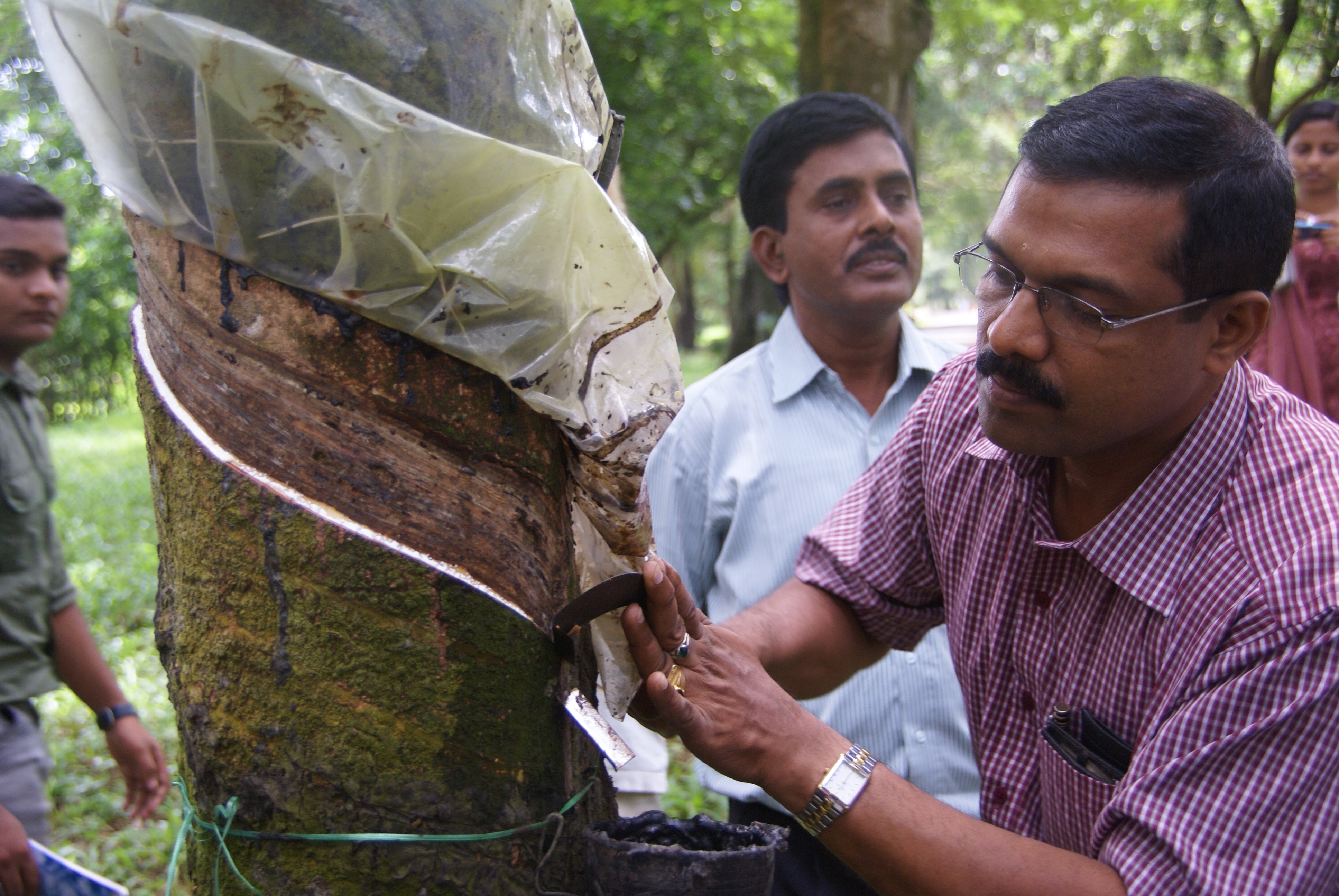
The biggest losses in rubber processing occur in the process, in the quality and quantity of product. The trees give off latex. However, this latex often has small pieces of tree bark and other impurities in it - reducing quality after processing. The latex also collomerates very quickly, so after the farmer cuts all the trees (it usually takes about 2 hours for 400 trees for a skilled worker), they quickly need to collect and process it. After this time, latex is still flowing out of the tree - this gets collected early the next morning as low grade rubber. The latex that is processed is either processed by the farmer directly or sent away for processing. If the farmer directly processes it, generally the latex is turned into rubber sheets. If it is sent away, it is preserved (temporarily!) with ammonia. This ammonia became an even bigger problem at one of our next visits, so I’ll blog about that soon too.
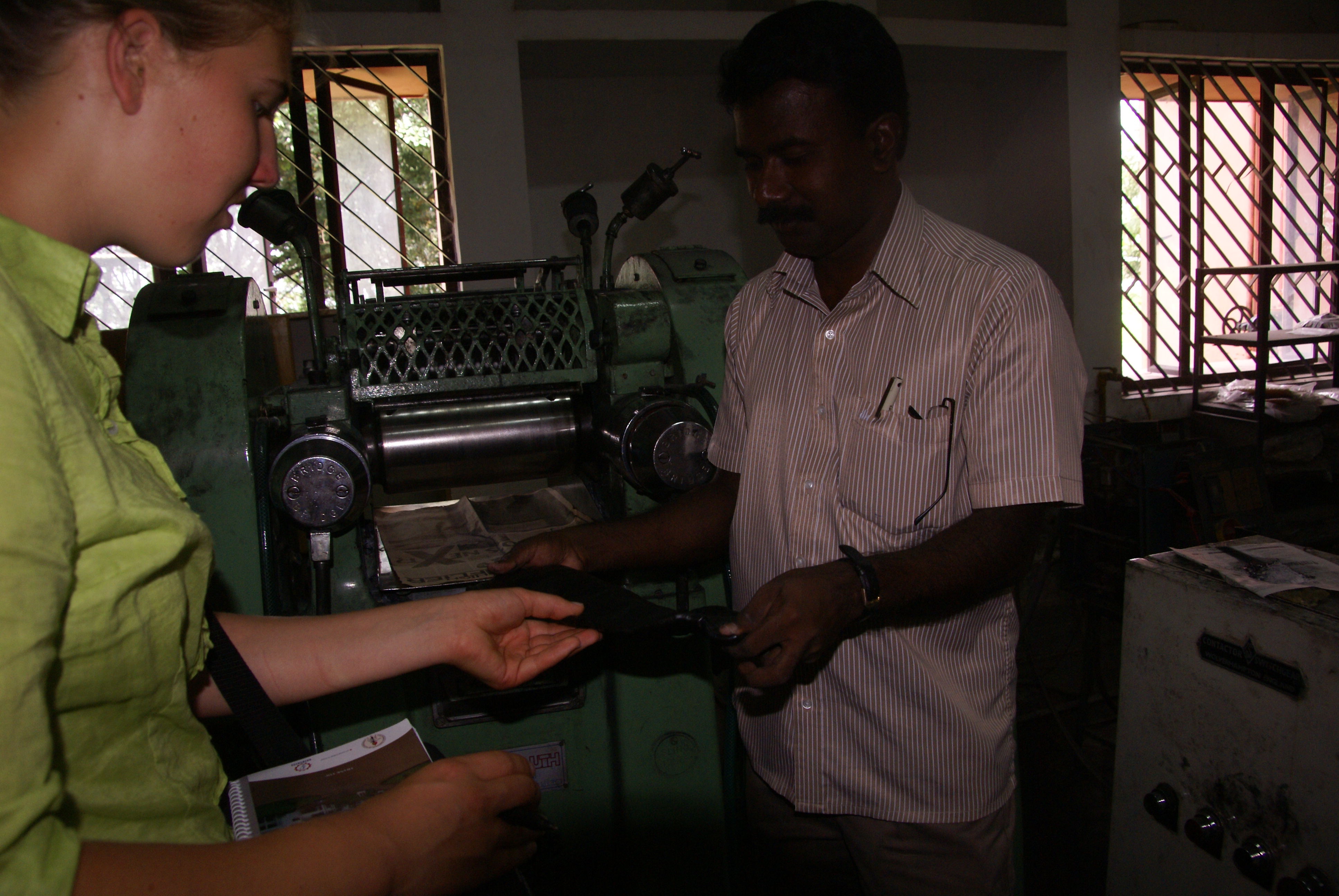
RRI also oversees the ACRT (advanced center for rubber technologies). They employ 130 scientists and engineers. They told us a lot about rubber processing and the different types of rubber; we even got to see some yellow rubber turn into tire material! A big problem with impurities in the rubber, they pointed out, was that as materials like tires underwent stress, small impurities generated a lot of tire strain.
The three major problems we identified at RRI were the need of a rubber tapping tool that doesn’t require as much skilled labor; improved rubber quality with less impurities; and the time with which rubber collomerates.
Because the rubber industry is so important in Kerala, we had several more rubber-related industry visits. Because many of the places we visited are small, and to cover more ground, we split into two teams for many of these. I ultimately only visited one other rubber-related industry, Thazhathethil Enterprises. TE is a small scale firm which manufacturs rubber mats from tires.
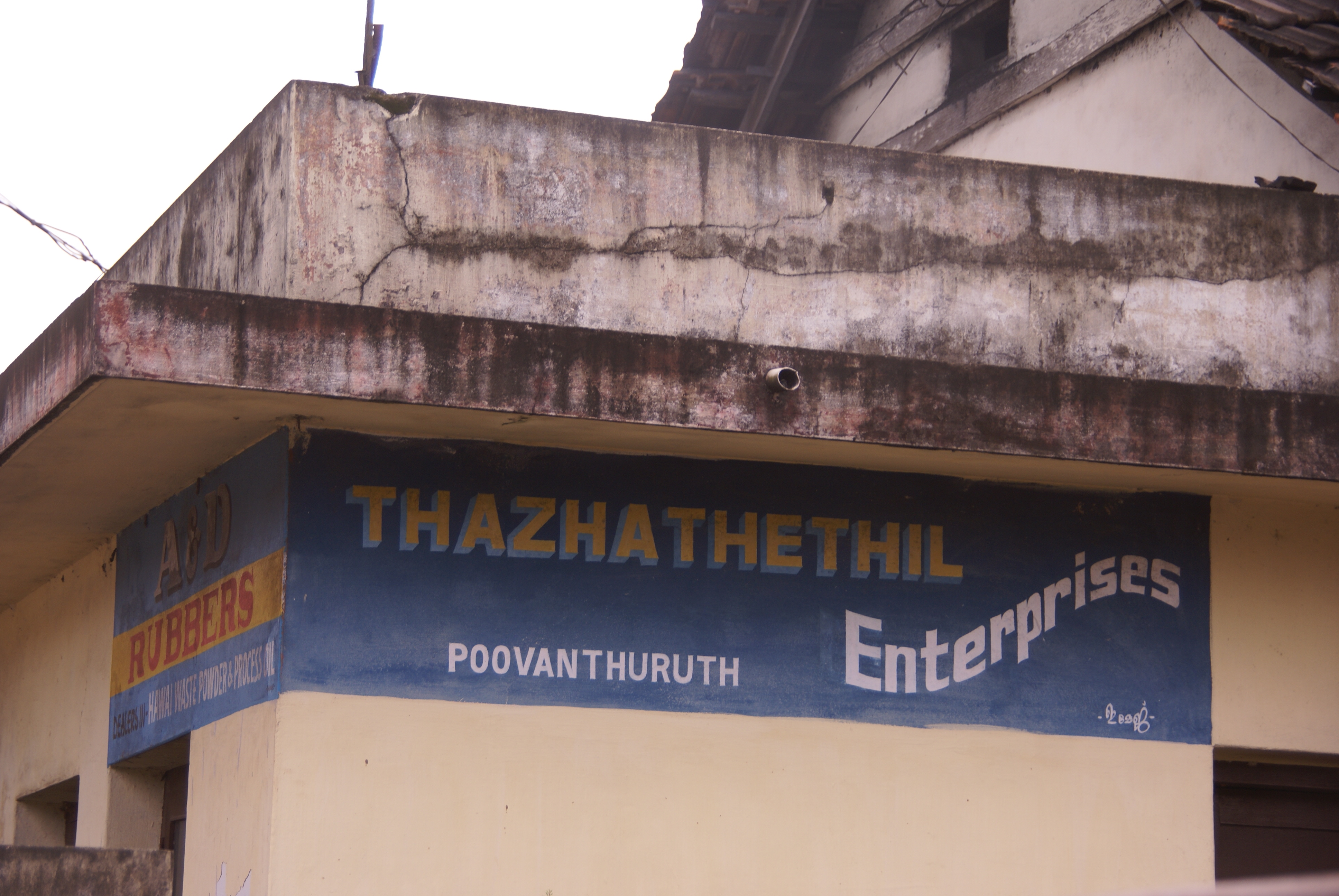
They literally cut up these huge tires, and then have a set of three machines to make them into rubber. First, one machine grinds them into about 1 cm large pieces. Another machine then grinds them more and a filter machine gets rid of the big pieces. A third machine grinds them finely and generates the product.
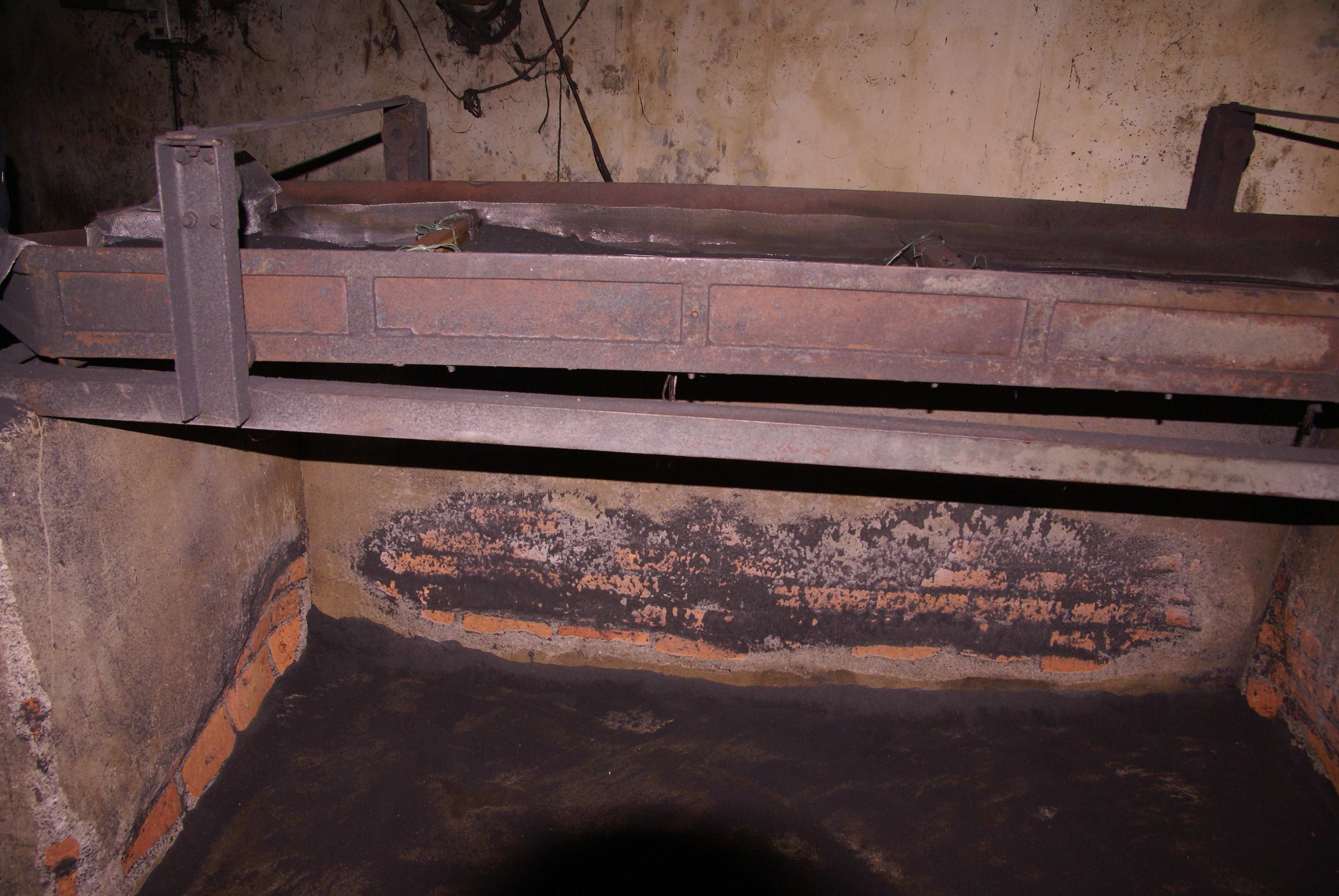
There’s just one little problem. Tires have metal straps in them. In all the griding processes, there is no way to remove this metal. Many of the companies working with old tires in the area have this problem. The company added a magnet to their system, but it only takes out 40% of the metal. In the finely, finely shredded rubber, you can still see tiny metallic pieces.
So, what’s the problem? You can barely see the metal in the rubber. When they make the mats, people won’t really see the metal. It takes about 10 days of wear and tear to notice the metal. The rubber wears down but the metal doesn’t, and if people are barefoot… you get the story. This metal needs to be removed from the rubber, but the magnet isn’t doing it. The company doesn’t have enough resources to buy another magnet or to send the rubber through the machine several times. They, and other companies like theirs working with old tires and old rubber products, are at risk of going out of business.
This problem really intrigues me for several reasons. Firstly, using the old tires to make mats is recycling the material, and I would rather see the tires used for that then end up in landfills (one thing I noticed in the places we visited, incidentally, is that they reuse or recycle so much more than we do in the US; there is way less trash!). Secondly, there are, the SAINTGITS students said, many of these kinds of entrepresises and they are all struggling with this problem; even more, removing metal from anything is a very common problem and finding a simply seperation process is a very basic problem. Finally, it’s a cool project and if it can’t be, financially, based on magnetism, we’re going to have to dig deep into the properties of these different materials and into their system as a whole!
With our three principles in mind, we visited not only these rubber-related organizations but many different industries – I’ll be blogging more about them in the upcoming weeks!