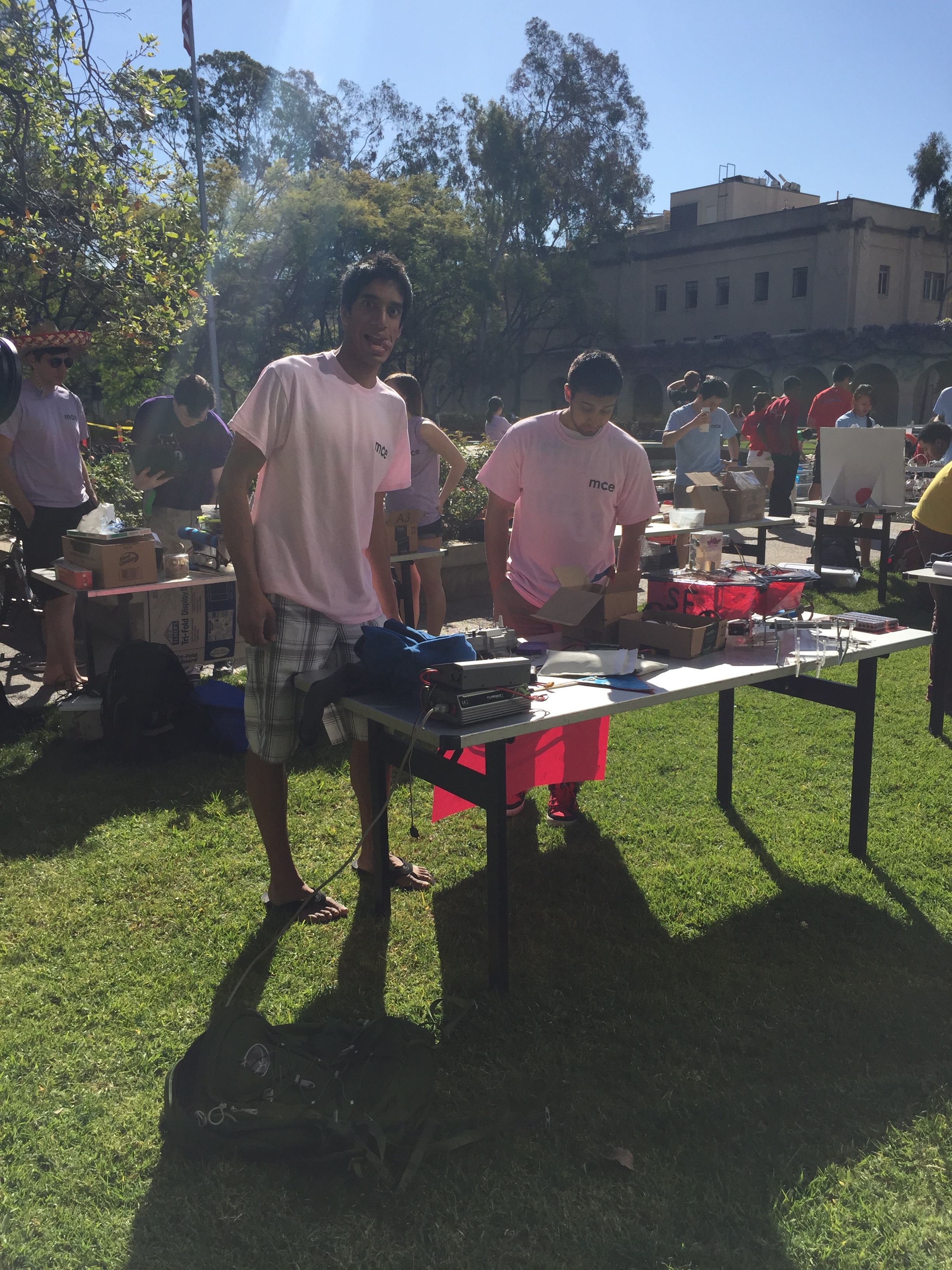
ME 72 Swimming Robot Competition!
At the end of last term, the ME 72 (mechanical engineering project class) had their final projects due. The project, spanning first and second term, was to build an amphibious robot that could play a water-based game against another team of robots. I took a ton of pictures of the competition, which was held at Millikan pond in front of the library. Hundreds of elementary school kids from Pasadena showed up to watch! And a couple of news crews. I guess “Caltech robots” generates a lot of interest :P
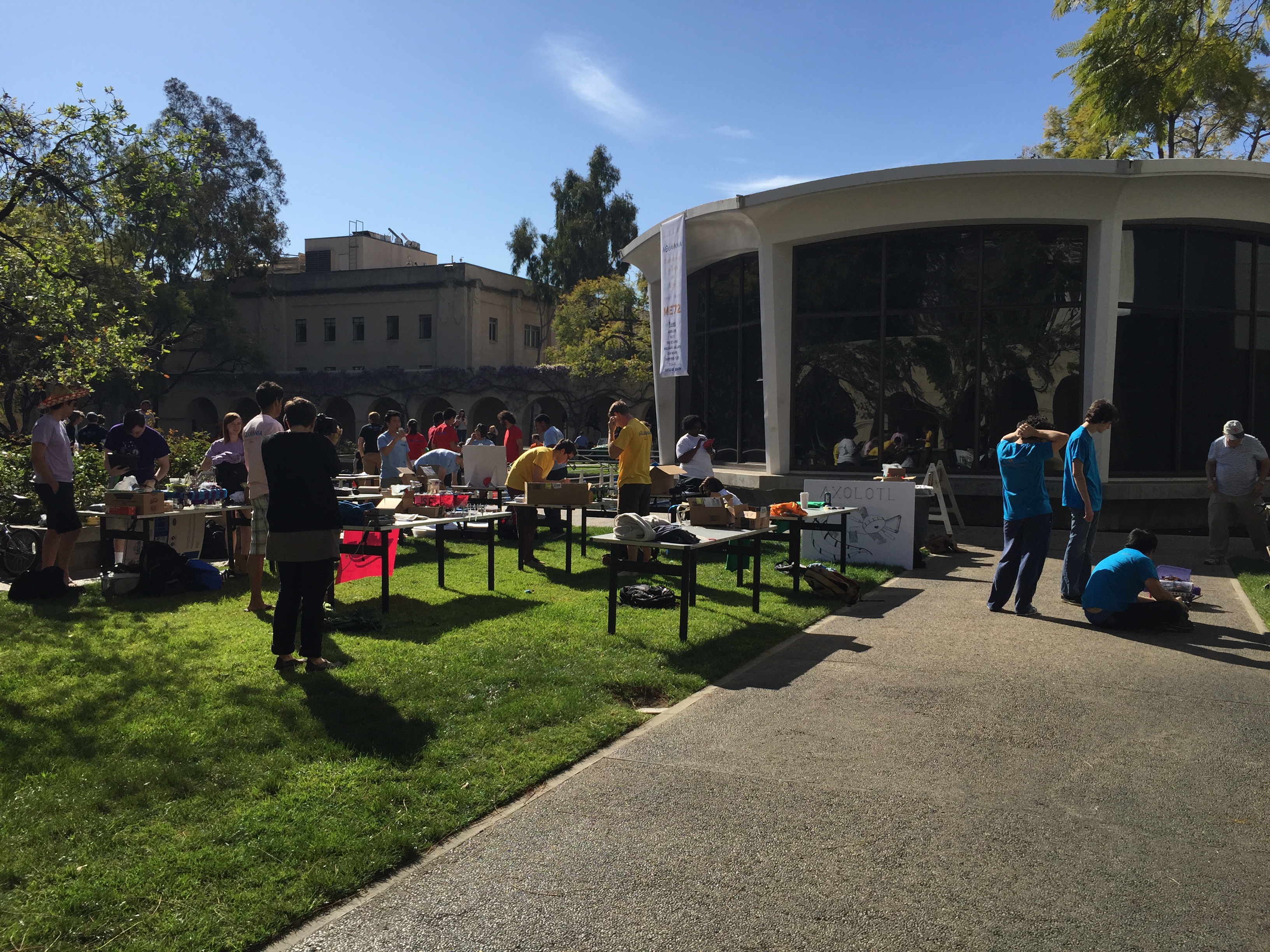
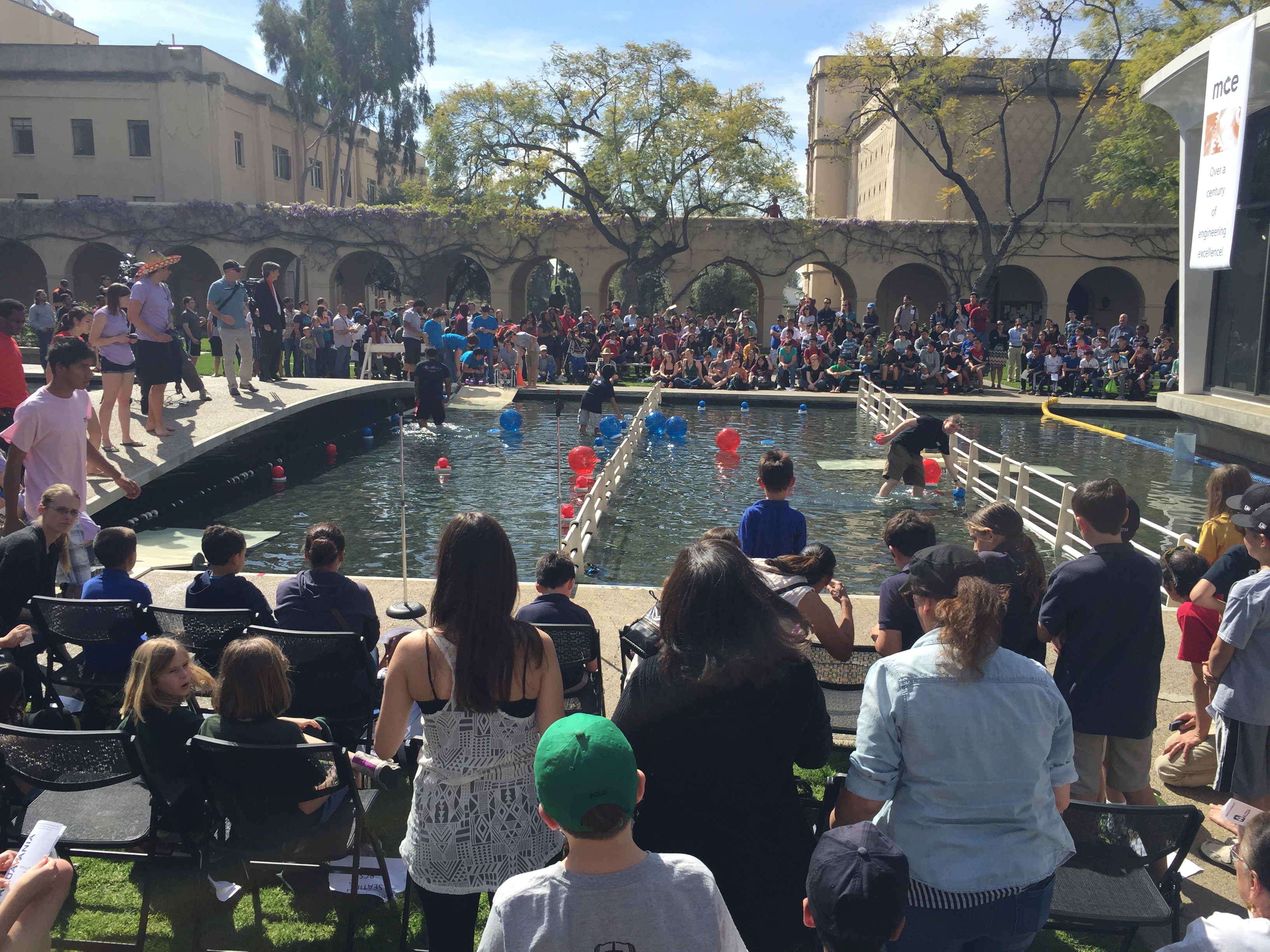
I also got a Q&A with my friend Rob, who was in the class, so you guys have a better idea of what this MechE class is like.
1. How much time did you have to build your robots? What were the guidelines, and what machines/prototyping methods did you use?
So we began the discussion early on during fall term. We were given the task to design a robot that can maneuver seamlessly between land and water to move different sized balls into higher scoring zones of the playing field. This meant, we began outside of Milikan Pond and entered the water via a ramp to begin play. If this part was done autonomously, teams could gain extra points. Once in the pond, we could move around and bring these balls to the other side of the pond. More points were earned if the teams could cross a land bridge to bring the balls to the farthest zone. After 5 min, then the teams had to make their way back to the starting positions to try and earn the last available points.
To accomplish this task, we were constrained to design a robot that could fit into a 18” square box at the start of the round with an $800 budget. We went through many iterations in design as we continued to test and compete in the mock challenges leading up to the final event. We primarily used the water jet and laser cutter to precisely cut our aluminum and acrylic pieces, respectively. Some additional modifications were needed on these pieces to acquire greater precision. These were done on the mills and lathes.
2. What was your budget? Did you have to Macgyver anything to get your robot to work?
$800. We definitely had to think of some quick fixes. Super glue and duct tape came in very handy in these situations. Leading up to the practice runs, we ran into some issues where we had to quickly use epoxy and left over plastic to fix a hole that sprung in our boat when we hit a part of the playing field.
3. What was the hardest thing to build? What the most challenging part of the class?
The hardest part to build was the waterproof impeller system. Our boat utilized an impeller, similar to that of a jet ski, to increase the performance of the propeller by funneling the propelled water. We had to somehow transmit the power from the motor inside the hull to the propeller in the water. We utilized a custom 3D printed casing, waterproof bearings, and carefully applied water tight caulking to successfully waterproof our power train.
The most challenging part of the class was to work effectively as a team towards the same goal. It was a great learning experience to be able to work through our different ideas and thought processes to produce our final robot as a combination of everyone’s contributions.
4. Have you done anything like this before? Are you taking any other classes like this at Caltech?
I took ME/EE/CS 75 my freshman year. This was the Caltech Solar Decathlon team where we built a house for the DOE 2013 competition in Irvine, CA. It was a similar experience, but on a much larger scale. We had around 20 techers all working on the same project, but split into different teams. Around the same time as 72 started, I decided to start a club to design and build two sustainable go karts. We are still working on this project and aim to enter the 2016 SAE Formula Electric competition. Working on these projects has been a lot of fun and I look forward to carrying what I have learned into my next ventures.